The I/O bus is the I/O data bus for the I/O modules. Through this bus, I/O and diagnosis data are transferred between the processor module and the I/O modules. Up to 10 I/O modules can be added.
The synchronized I/O bus is the I/O data bus for the I/O modules connected with the processor modules or communication interface modules. Through this bus, I/O and diagnosis data are transferred.
With its fast data transmission, the I/O bus obtains very low reaction times.
Up to 10 I/O terminal units (for one I/O module each) can be added to one terminal base or to one AC500-eCo processor module. The I/O terminal units and the AC500-eCo I/O modules, have a bus input at the left side and a bus output at the right side. Thus the length of the I/O bus increases with the number of attached I/O modules⮫ Table 135 “Maximum number of I/O devices which can be connected to the I/O bus”.
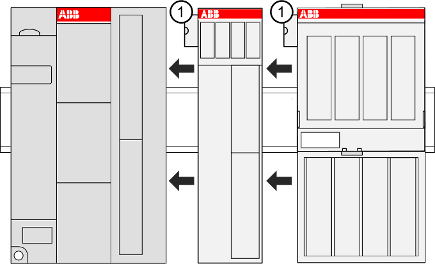
- 1
-
I/O bus connection
The connection of the I/O bus is performed automatically by telescoping the modules on the DIN rail.
The I/O bus provides the following signals:
-
Supply voltage of 3.3 V DC for feeding the electronic interface components.
-
3 data lines for the synchronized serial data exchange.
-
Several control signals.
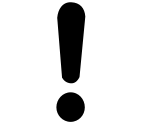
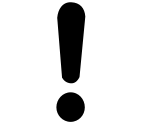
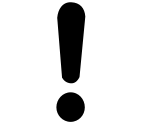
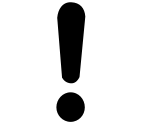
NOTICE
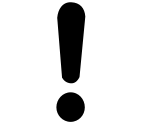
Except when using hot swap terminal units, the I/O bus is not designed for pulling and plugging modules during operation.
If a module is pulled or plugged on a terminal unit that is not hot swap capable while the bus is running, the following consequences are possible.
-
Reset of the station or of the processor module.
-
System lockup.
-
Damage of the module.
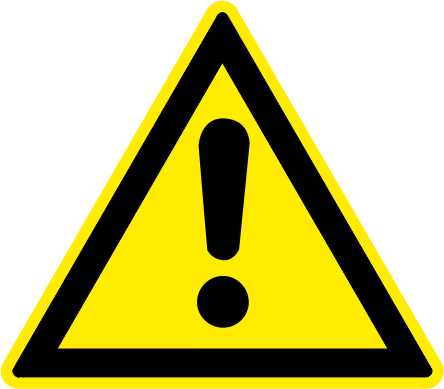
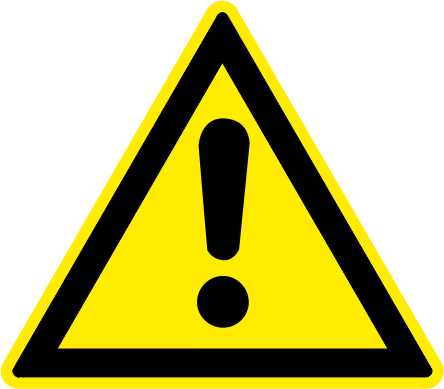
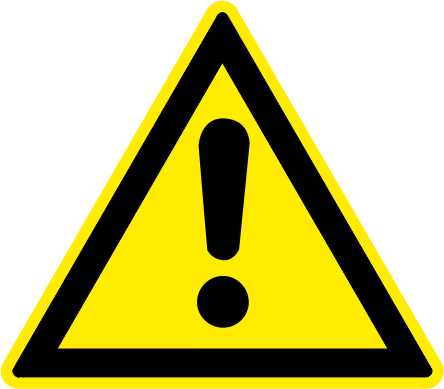
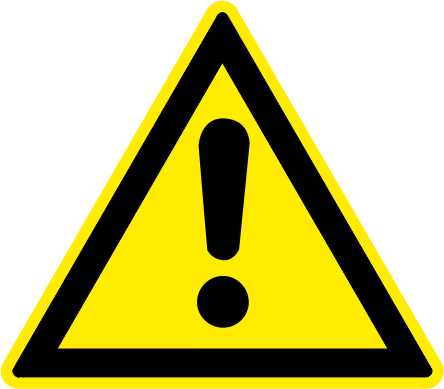
WARNING
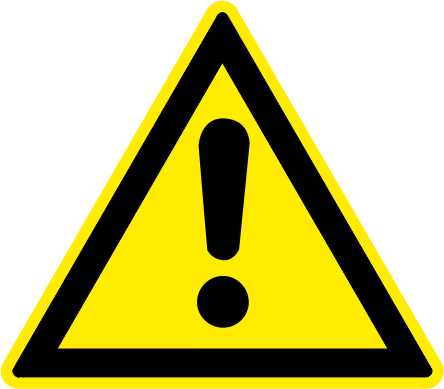
Removal/Insertion under power
Removal or insertion under power is permissible only if all conditions for hot swapping are fullfilled.
⮫ “Replace an I/O module with hot swap”
The devices are not designed for removal or insertion under power when the conditions for hot swap do not apply. Because of unforeseeable consequences, it is not allowed to plug in or unplug devices with the power being ON.
Make sure that all voltage sources (supply and process voltage) are switched off before doing any of the following actions:
-
Connect or disconnect any signal or terminal block.
-
Remove, mount or replace a module.
Disconnecting any powered devices while they are energized in a hazardous location could result in an electric arc, which could create an ignition source resulting in fire or explosion.
Prior to proceeding, make sure that power is been disconnected and that the area has been thoroughly checked to ensure that flammable materials are not present.
The devices must not be opened when in operation. The same applies to the network interfaces.
Profibus (master and slave) and CM589-PNIO are available since version 2.5.0 of the Automation Builder.
Device |
Version Automation Builder |
Version firmware |
Max. number of I/O devices |
---|---|---|---|
CANopen bus modules CI581-CN and CI582-CN |
As of V2.1.0 |
All |
0 |
PROFINET bus modules CI501-PNIO and CI502-PNIO |
As of V2.1.0 |
all |
10 |
EtherCAT communication interface module CI511-ETHCAT and CI512-ETHCAT |
As of V2.1.0 |
As of V2.0.x |
10 |
Modbus communication interface module CI521 and CI522 |
Independent from Automation Builder version |
all |
10 |
Profibus (master and slave) and CM589-PNIO are available since version 2.5.0 of the Automation Builder.
Parameter |
Value |
---|---|
Supply voltage, signal level |
3.3 V DC ± 10 % |
Max. supply current |
On request |
Type of the data interface |
Synchronized serial data exchange |
Bus data transmission speed |
1.8 Mb/s |
Minimum bus cycle time |
500 µs This value is valid for all module combinations (from 1 to 10 I/O modules) |
Galvanic isolation |
I/O bus is galvanic connected to CPU and communication interface logic ciruits. Galvanic isolation of I/O bus is I/O module specific. See each module specification for details. |
Protection against electrostatic discharge (ESD) |
TB5xx, TB56xx: with protection diodes, no ESD discharge allowed on the port. |
Parameter |
Value |
---|---|
Bus connection |
Left-side and right-side connection from module to module via a 10-pole HE plug (male at the left side, female at the right side) |
Mechanical connection |
Established by the terminal units |
Max. bus length |
1 m |