Automation Builder supports the Tool Calling Interface (TCI) up to conformance class 3 to engineer 3rd party safety devices.
The TCI from PROFINET organization offers a standard interface to call 3rd party configuration tools to
e.g., configure iParameters in functional safety applications, calculate F_iPar_CRC
values and write configurations via the PLC to the safety devices.
The corresponding vendor specific configuration tools must be installed manually on the same PC as the Automation Builder. As soon as a 3rd party safety device is added to the Automation Builder project and a matching configuration tool is found to be installed, corresponding context menus are offered on the device to call this tool via TCI (refer to screenshot below).
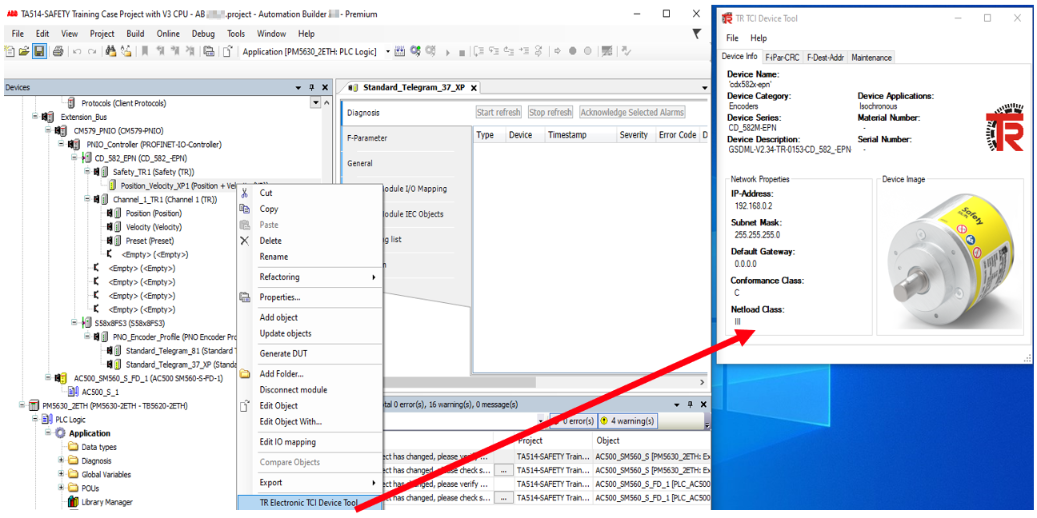
The offered functionality of those configuration tools strongly varies on the device manufacturer. In the following the functionalities and workflows are exemplarily shown with two tools.
TR TCI Device Tool
-
Install the “TR TCI Device Tool” on the same PC as the Automation Builder.
-
Install the required TR GSDML-files in the Automation Builder device repository.
-
Create the desired devices configuration in the Automation Builder device tree.
-
Define the required iParameter of the TR safety device in the Automation Builder.
-
Open the “TR TCI Device Tool” via context menu on the TR safety device.
-
Calculate the
F_iPar_CRC
in the “TR TCI Device Tool” and paste the value into the corresponding field in the Automation Builder editor.
In case an online connection is available you can also display the F-Destination-Address which can be set via rotary switches depending on the used hardware device and read/write maintenance data.
To enable an online connection, you must be online in Automation Builder, PLC needs to be in RUN and PROFINET must be running.
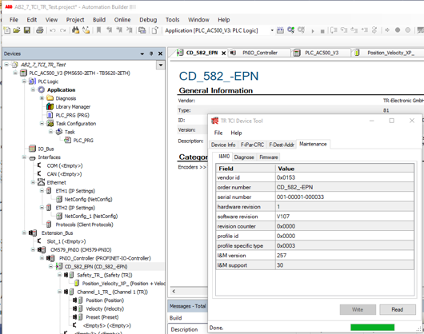
Siemens F-Destination-Address Assign Device Tool
-
Install the Siemens S7-Failsafe Configuration Tool on the same PC as the Automation Builder.
-
Install the required Siemens GSDML-files in the Automation Builder device repository.
-
Create the desired devices configuration in the Automation Builder device tree.
-
Change “F_Dest_Add” or “F_Source_Add” on the Siemens safety device in the Automation Builder project.
-
Set “F_Dest_Add” and “F_Source_Add” (if needed in offline mode).
-
Go online, PLC needs to be in RUN and PROFInet must be running.
-
Call the Siemens device tool and choose your preferred way of identification (LED blinking or serial number).
-
Select the check box at the module where the F-destination-address should be set.
-
Press the [Identification] button.
-
Press the [Assign PROFIsafe-address] button after you confirmed that either the correct module is blinking or the displayed serial numbers is matching.
The device tool has a build in timeout with only a view seconds. After that time the device tool cannot communicate with the slave anymore. In this case close the device tool and reopen it again.