With PS5611-Motion the application program and the profile generator are realized in the PLC. The implementation of the profile generator is based on a set of function blocks which are named central motion control (CMC).
The profile generator of many possible axes is centrally placed inside the AC500 PLC. Therefore multiaxis motion functionalities become easily available and can be accessed by PLCopen function blocks. As a result, motion control functionalities are almost drive independent.
The detailed functionality of each function block is defined in the integrated documentation of the library.
Available motion control functionalities:
-
Simple axis Movements
-
Electronic Gearin
-
Electronic CAMs
-
Position Profiles
-
Velocity Profiles
-
Acceleration Profiles
-
Load control (Torque profilling)
Then the output is a position reference signal which the drive will follow. A new position reference value will be calculated with every cycle of the PLC and has to be transferred to the drive, which demands real time capabilities to the PLC and to the communication channel. A real time fieldbus like EtherCAT is needed. The feedback of the actual position can be used for supervision purposes during operation and is needed to adjust the value of the position reference before the drive will be enabled.
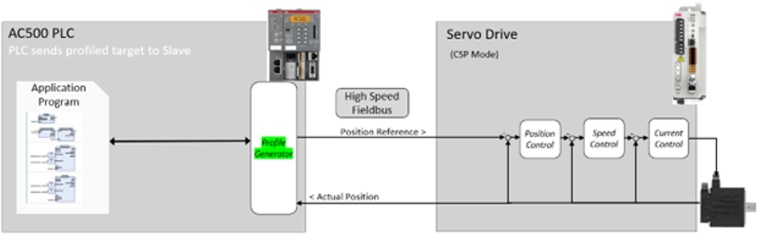
With PLC-based motion control it is also possible to include the position control loop to the AC500 PLC. In this case a speed reference signal will be transferred to the drive, which makes it possible to perform the full range of motion functionalities with standard drives. To close the position control loop, feedback of the actual position is mandatory.
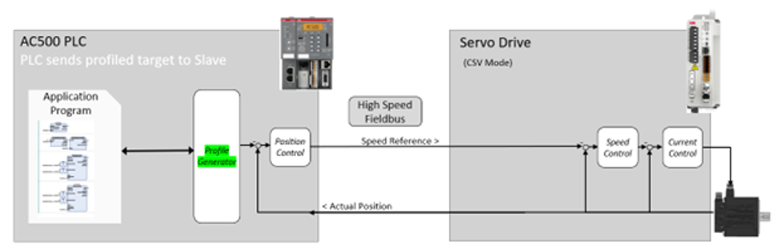
With PLC-based motion control it is also possible to include the load control loop to the AC500 PLC. In this case a speed reference signal will be transferred to the drive, which makes it possible to perform the full range of motion functionalities with standard drives. To close the position control loop, feedback of the actual position is mandatory and to close the load control loop, feedback of the actual load / torque is mandatory.
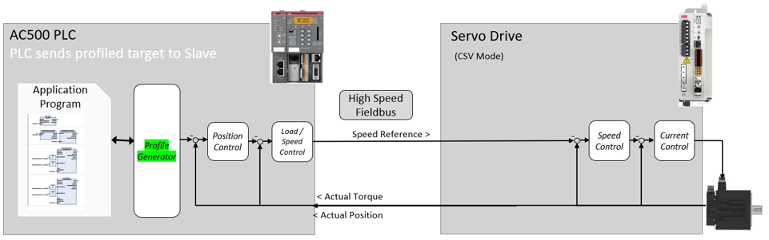
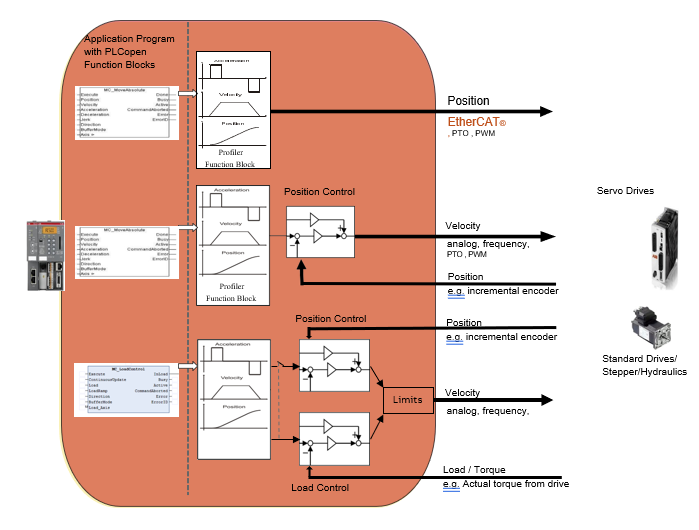